Mastering Composite Structures Design in CATIA: A Comprehensive Guide
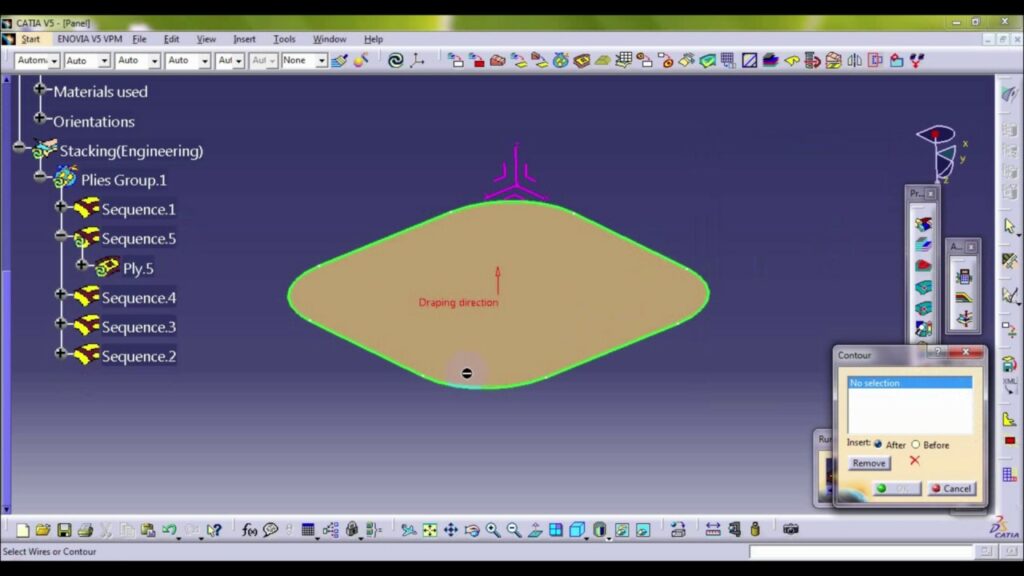
Introduction: Composite materials have become increasingly popular in engineering applications due to their unique properties, including high strength-to-weight ratio, corrosion resistance, and design flexibility. CATIA, developed by Dassault Systèmes, is a leading software suite widely used for computer-aided design (CAD), engineering (CAE), and manufacturing (CAM) across various industries. In this comprehensive guide, we will delve into the intricacies of designing composite structures in CATIA, covering everything from material selection and laminate design to analysis and manufacturing preparation.
Section 1: Understanding Composite Materials 1.1 Overview of Composite Materials: Composite materials are engineered materials composed of two or more constituent materials with significantly different physical or chemical properties. Common types of composite materials include fiber-reinforced polymers (FRP), carbon fiber composites, and glass fiber composites. Composite structures offer superior mechanical properties, durability, and corrosion resistance compared to traditional materials such as metals and plastics.
1.2 Advantages of Composite Structures: Composite structures offer several advantages over conventional materials, including:
- High Strength-to-Weight Ratio: Composite materials combine lightweight fibers with high-strength resins, resulting in structures that are stronger and lighter than traditional materials.
- Design Flexibility: Composites can be molded into complex shapes, allowing designers to optimize structural performance and aerodynamic efficiency.
- Corrosion Resistance: Composite materials are inherently resistant to corrosion, making them ideal for marine, aerospace, and automotive applications.
- Tailored Properties: By varying the type, orientation, and volume fraction of reinforcement fibers, engineers can tailor the mechanical properties of composite structures to meet specific design requirements.
Section 2: Introduction to CATIA Composite Design 2.1 Overview of CATIA: CATIA (Computer-Aided Three-Dimensional Interactive Application) is a comprehensive CAD/CAM/CAE software suite developed by Dassault Systèmes. CATIA provides a range of modules and tools for product design, engineering analysis, and manufacturing planning across various industries, including aerospace, automotive, and consumer goods.
2.2 CATIA Composite Design Workbench: CATIA offers a dedicated Composite Design workbench, allowing engineers to design, analyze, and manufacture composite structures within a unified environment. The Composite Design workbench provides tools for defining material properties, creating laminate layouts, simulating behavior, and generating manufacturing data for composite parts.
Section 3: Material Selection and Definition 3.1 Material Database: CATIA includes a comprehensive material database containing properties for various composite materials, including fibers, resins, and matrices. Engineers can select materials from the database or define custom material properties based on manufacturer specifications or test data.
3.2 Material Properties: In CATIA, engineers define material properties such as elastic modulus, Poisson’s ratio, and strength characteristics for each constituent material in the composite laminate. Material properties influence the structural behavior, mechanical performance, and failure modes of composite structures, making accurate characterization essential for design optimization.
Section 4: Laminate Design and Layup 4.1 Laminate Definition: In CATIA, engineers create composite laminates by defining the stacking sequence, fiber orientations, and ply thicknesses for each layer of the laminate. CATIA provides tools for visualizing laminate layouts, specifying ply boundaries, and managing material orientations to ensure optimal structural performance.
4.2 Ply Creation and Editing: CATIA allows engineers to create, edit, and manipulate individual plies within the composite laminate. Engineers can adjust ply orientations, add reinforcement patches, and modify ply boundaries to optimize load transfer, minimize stress concentrations, and improve overall laminate performance.
Section 5: Analysis and Simulation 5.1 Finite Element Analysis (FEA): CATIA offers integration with finite element analysis (FEA) tools for simulating the structural behavior of composite structures under various loading conditions. Engineers can perform static, dynamic, and nonlinear analyses to evaluate stress distributions, deformation patterns, and failure modes in composite components.
5.2 Laminate Analysis: CATIA provides tools for analyzing laminate properties such as stiffness, strength, and failure criteria based on classical lamination theory (CLT) or advanced numerical methods. Engineers can calculate laminate properties, such as bending stiffness, shear modulus, and interlaminar stresses, to assess structural performance and verify design compliance.
Section 6: Manufacturing Preparation 6.1 Ply Cutting and Nesting: CATIA facilitates the preparation of composite parts for manufacturing by generating ply cutting patterns and nesting layouts for automated cutting machines. Engineers can optimize ply orientations, minimize material waste, and maximize material utilization by nesting plies efficiently within the raw material sheets.
6.2 Manufacturing Documentation: CATIA generates manufacturing documentation, including ply schedules, cutting patterns, and layup instructions, to guide production processes and ensure quality control. Engineers can export manufacturing data in standard formats, such as DXF (Drawing Exchange Format) or CNC (Computer Numerical Control), for seamless integration with manufacturing systems.
Section 7: Real-World Applications and Case Studies 7.1 Aerospace Structures: In the aerospace industry, CATIA is extensively used for designing composite structures for aircraft fuselages, wings, and empennages. Engineers leverage CATIA’s advanced modeling and analysis capabilities to optimize composite layups, reduce structural weight, and improve fuel efficiency in aerospace applications.
7.2 Automotive Components: CATIA plays a crucial role in automotive design and engineering, particularly in the development of lightweight composite components for vehicles. Engineers use CATIA to design composite body panels, chassis components, and interior trim parts, leveraging composite materials to enhance vehicle performance, fuel economy, and crash safety.
Section 8: Best Practices and Optimization Strategies 8.1 Design for Manufacturability: To ensure manufacturability and cost-effectiveness, engineers should consider manufacturing constraints and process limitations during the design phase. CATIA facilitates design for manufacturability (DFM) by providing tools for optimizing ply orientations, minimizing material waste, and streamlining production workflows.
8.2 Multidisciplinary Collaboration: Effective collaboration among design, analysis, and manufacturing teams is essential for successful composite design projects. CATIA supports multidisciplinary collaboration by providing a unified platform for sharing design data, exchanging feedback, and coordinating design changes across different departments and disciplines.
Section 9: Future Trends and Developments 9.1 Advanced Simulation Techniques: Future developments in CATIA may include advanced simulation techniques for predicting the behavior of composite structures under extreme conditions, such as impact, fatigue, and environmental degradation. Engineers may leverage advanced modeling methods, such as cohesive zone modeling and progressive failure analysis, to simulate complex failure modes and damage propagation in composite materials.
9.2 Additive Manufacturing Integration: With the rise of additive manufacturing technologies, CATIA may integrate support for designing composite structures optimized for 3D printing. Engineers may use CATIA to generate lattice structures, topology-optimized designs, and functionally graded materials, leveraging the benefits of additive manufacturing for lightweight, high-performance composite components.
Conclusion: CATIA provides a comprehensive suite of tools and capabilities for designing composite structures across various industries, from aerospace and automotive to marine and consumer goods. By mastering the techniques and best practices outlined in this guide, engineers can leverage CATIA’s advanced features to create innovative, lightweight composite components that meet stringent performance, cost, and manufacturing requirements. With its intuitive interface, robust analysis tools, and seamless integration with manufacturing processes, CATIA continues to be a preferred choice for composite design and engineering in an increasingly competitive global market.