Unlocking Design Optimization: A Comprehensive Guide to Enhancing Structural Integrity in SolidWorks
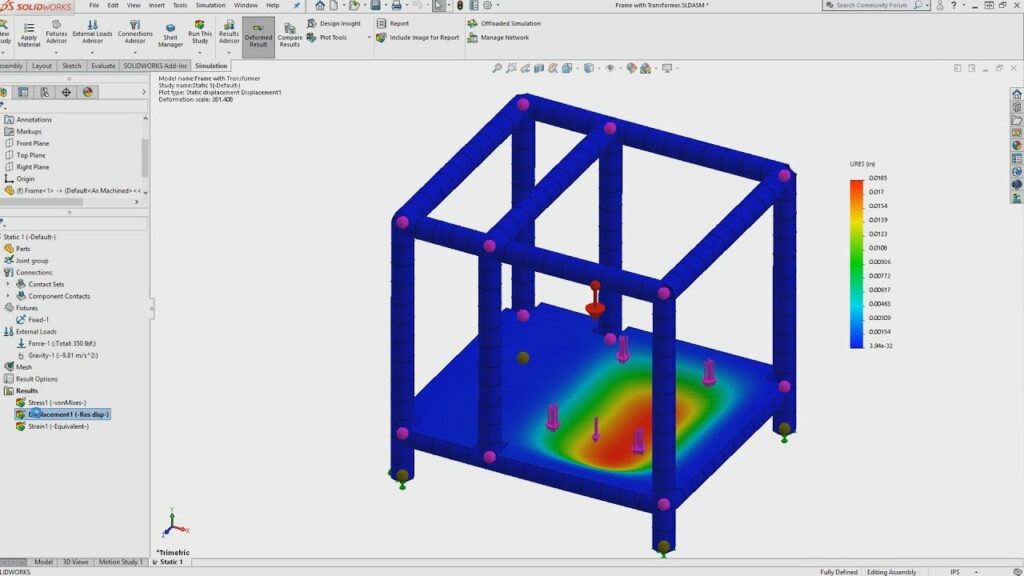
In the realm of engineering and design, optimizing a design for structural integrity and performance is a crucial endeavor. SolidWorks, a leading 3D CAD software, equips designers and engineers with powerful tools to analyze stress distribution and deformation in their models. Interpreting stress analysis results in SolidWorks provides valuable insights into areas of concern and opportunities for improvement. In this extensive guide, we will explore the step-by-step process of optimizing a design based on stress analysis results in SolidWorks, covering everything from identifying weaknesses to implementing design modifications and validating improvements.
1. Understanding Stress Analysis Results:
- Before diving into optimization, it’s essential to thoroughly understand the stress analysis results obtained from SolidWorks simulations.
- Stress distribution, deformation, safety factors, and stress concentration areas provide valuable insights into the behavior of the design under different loading conditions.
2. Identifying Weaknesses and Stress Hotspots:
- Start by identifying weaknesses and stress hotspots in the design based on stress analysis results.
- Areas of high stress concentration, excessive deformation, or low safety factors indicate potential areas for improvement.
- SolidWorks’ visualization tools, such as contour plots and stress plots, facilitate the identification of critical areas requiring attention.
3. Analyzing Design Constraints and Requirements:
- Consider the design constraints, requirements, and performance objectives when planning optimization strategies.
- Evaluate factors such as material properties, manufacturing constraints, cost considerations, and functional requirements.
- Ensure that optimization efforts align with the overall design goals and project specifications.
4. Generating Design Alternatives:
- Generate design alternatives or iterations based on identified weaknesses and optimization goals.
- Use SolidWorks’ parametric modeling capabilities to explore different design configurations, geometry variations, and material options.
- Experiment with design parameters such as thickness, geometry, fillet radii, and material properties to evaluate their impact on structural performance.
5. Implementing Design Modifications:
- Implement design modifications and enhancements based on the insights gained from stress analysis results.
- Make changes to the model geometry, material properties, or loading conditions to address identified weaknesses and stress hotspots.
- SolidWorks provides intuitive modeling tools for making design modifications efficiently and accurately.
6. Iterating and Refining the Design:
- Iterate on the design by evaluating the performance of each iteration through simulation and analysis.
- Refine the design iteratively by making incremental improvements and assessing their impact on structural integrity and performance.
- SolidWorks’ simulation-driven design approach enables users to iterate rapidly and efficiently, exploring multiple design alternatives to find the optimal solution.
7. Validating Design Improvements:
- Validate design improvements through simulation, physical testing, or comparison with empirical data.
- Use SolidWorks’ simulation tools to verify that design modifications effectively address identified weaknesses and improve structural performance.
- Compare simulation results of optimized designs with baseline models to quantify improvements and validate the effectiveness of optimization efforts.
8. Documenting Optimization Process and Results:
- Document the optimization process, design iterations, and results to provide a clear record of the improvement journey.
- Create comprehensive reports and documentation detailing the optimization strategies employed, design modifications made, and resulting performance improvements.
- Use visualizations, tables, charts, and annotations to communicate optimization findings effectively to stakeholders.
9. Implementing Final Design:
- Once optimization goals are achieved and design improvements are validated, implement the final optimized design.
- Ensure that the optimized design meets all project requirements, including structural integrity, performance, manufacturability, and cost constraints.
- SolidWorks provides tools for generating manufacturing drawings, assembly instructions, and documentation to facilitate the implementation of the final design.
10. Conclusion:
- Optimizing a design based on stress analysis results in SolidWorks is a systematic and iterative process that requires careful consideration of design constraints, objectives, and performance requirements.
- By following the steps outlined in this guide and leveraging SolidWorks’ simulation-driven design capabilities, users can optimize designs for maximum structural integrity and performance.
- Whether designing mechanical components, structural assemblies, or complex systems, SolidWorks empowers users to optimize designs with confidence, ensuring they meet the highest standards of quality, reliability, and efficiency.