Demystifying Stress Analysis Results Interpretation in SolidWorks: A Comprehensive Guide
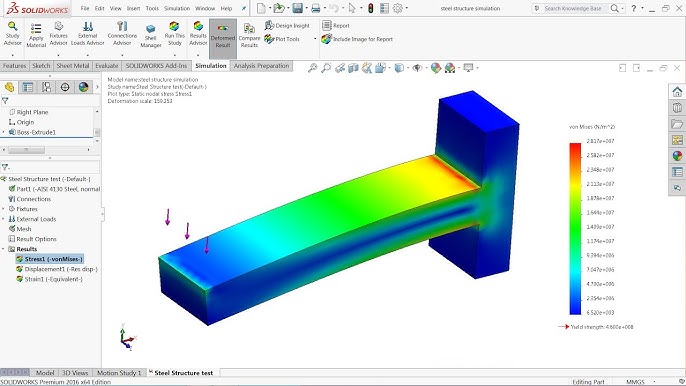
SolidWorks, a leading software in the realm of 3D CAD design, offers powerful simulation tools that enable engineers and designers to analyze the behavior of their designs under various loading conditions. One critical aspect of simulation is interpreting the results accurately to gain insights into the structural integrity and performance of the model. In this extensive guide, we will delve into the step-by-step process of interpreting stress analysis results in SolidWorks, covering everything from understanding stress distribution to evaluating safety factors and optimizing designs.
1. Understanding Stress Analysis in SolidWorks:
- Stress analysis in SolidWorks involves simulating the response of a model to applied loads and boundary conditions.
- It provides valuable information about stress distribution, deformation, safety factors, and other mechanical properties of the model.
2. Accessing Stress Analysis Results:
- After running a stress analysis simulation in SolidWorks, access the results by opening the Simulation Study tab.
- Here, you’ll find a range of tools and options for visualizing and interpreting the results.
3. Visualizing Stress Distribution:
- One of the primary aspects of interpreting stress analysis results is visualizing stress distribution throughout the model.
- SolidWorks offers contour plots, color maps, and stress plots to visualize stress levels and gradients.
- Different colors represent varying stress magnitudes, allowing users to identify areas of high stress concentration.
4. Analyzing Deformation:
- Deformation analysis provides insights into how the model responds to applied loads.
- SolidWorks displays displacement plots and deformation animations to visualize how the model deforms under load.
- Excessive deformation in critical areas may indicate potential design flaws or areas requiring reinforcement.
5. Evaluating Safety Factors:
- Safety factors are critical in assessing the reliability and robustness of a design.
- SolidWorks calculates safety factors based on factors such as material properties, applied loads, and stress levels.
- A safety factor below 1 indicates potential failure, while a factor above 1 signifies a margin of safety.
6. Identifying Stress Hotspots:
- Stress hotspots are areas of the model experiencing high stress concentrations.
- SolidWorks allows users to identify stress hotspots by analyzing stress plots and contour plots.
- Addressing stress hotspots is crucial for optimizing the design and preventing premature failure.
7. Comparing Results to Design Specifications:
- Compare stress analysis results to design specifications and industry standards.
- Ensure that stress levels and safety factors meet or exceed design requirements.
- SolidWorks provides tools for generating reports and documentation to document and communicate results effectively.
8. Iterating on the Design:
- Based on the interpretation of stress analysis results, iterate on the design to optimize performance and reliability.
- Make design modifications to reduce stress concentrations, improve safety factors, and enhance overall performance.
- SolidWorks’ parametric modeling capabilities facilitate iterative design processes, allowing users to explore design alternatives and refine the model iteratively.
9. Validating Results:
- Validate stress analysis results through physical testing or comparison with empirical data.
- Conduct physical tests to verify the accuracy and reliability of simulation results.
- SolidWorks offers tools for comparing simulation results with experimental measurements and validating the simulation model.
10. Documenting Findings:
- Document the interpretation of stress analysis results, including observations, conclusions, and recommendations.
- Generate comprehensive reports and documentation to communicate findings to stakeholders effectively.
- Include visualizations, tables, charts, and annotations to support the interpretation and facilitate decision-making.
Conclusion:
- Interpreting stress analysis results in SolidWorks is a critical aspect of the design process, enabling engineers and designers to assess the structural integrity and performance of their models accurately.
- By following the steps outlined in this guide and leveraging SolidWorks’ powerful simulation tools, users can gain valuable insights into the behavior of their designs and make informed decisions to optimize performance and reliability.
- Whether designing mechanical components, structural assemblies, or complex systems, SolidWorks empowers users to interpret stress analysis results with confidence, ensuring designs meet the highest standards of quality and safety.