Mastering Rotary Axis Machining: A Comprehensive Guide for CNC Machinists
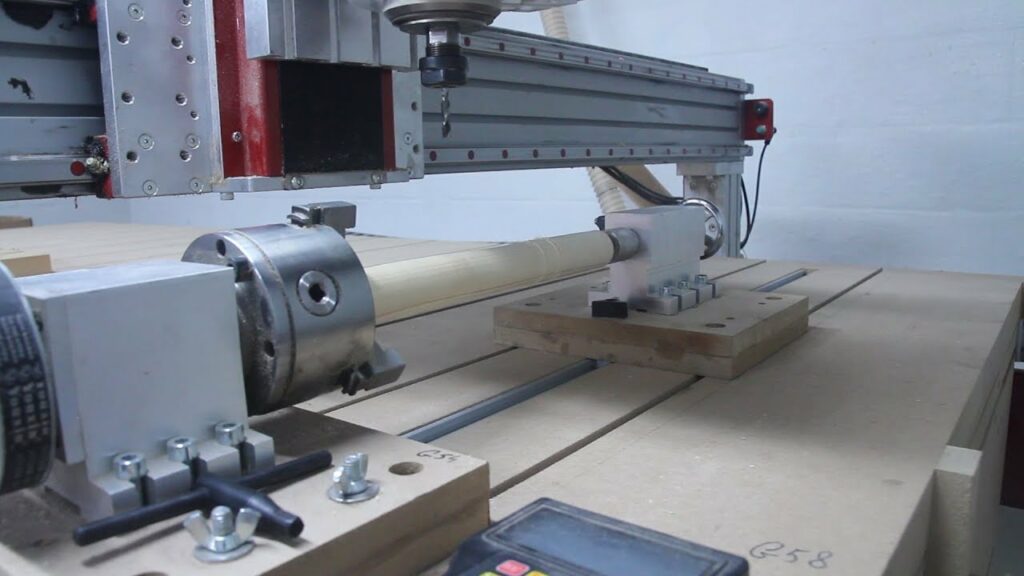
Introduction:
Rotary axis machining, also known as multi-axis or 4th/5th axis machining, is a powerful technique used in CNC (Computer Numerical Control) machining to produce complex parts with intricate geometries. By incorporating rotary axes into CNC machines, machinists can rotate workpieces along multiple axes simultaneously, allowing for machining operations on curved surfaces, contoured profiles, and non-linear features. In this comprehensive guide, we will delve into the intricacies of rotary axis machining, covering essential concepts, software options, workflow, best practices, and advanced techniques. Whether you’re a novice CNC machinist or an experienced professional seeking to expand your machining capabilities, this guide will equip you with the knowledge and skills necessary to master rotary axis machining effectively.
Understanding Rotary Axis Machining:
Rotary axis machining involves rotating workpieces around one or more axes of rotation to enable machining operations on multiple sides or surfaces of the workpiece. Common rotary axes configurations include the A-axis (rotating about the X-axis), B-axis (rotating about the Y-axis), and C-axis (rotating about the Z-axis). By integrating rotary axes into CNC machines, machinists can perform complex machining tasks such as milling, drilling, turning, and engraving on curved, contoured, or irregularly shaped surfaces. Rotary axis machining is commonly used in industries such as aerospace, automotive, medical, and manufacturing, where precision and versatility are paramount.
Selecting Suitable CNC Machine and Rotary Axis Configuration:
The first step in utilizing rotary axis machining is selecting a suitable CNC machine equipped with rotary axis capabilities. Various CNC machines, including vertical machining centers (VMCs), horizontal machining centers (HMCs), and multi-axis machining centers, offer options for integrating rotary axes into their configurations. When selecting a machine, consider factors such as the number of rotary axes (3-axis, 4-axis, or 5-axis), axis orientation (horizontal or vertical), table size, spindle power, and compatibility with CAD/CAM software. Choose a rotary axis configuration that aligns with the specific machining requirements and part geometries of your projects.
Analyzing Workpiece Geometry and Machining Requirements:
Before performing rotary axis machining, analyze the geometry and machining requirements of the workpiece to determine the most suitable approach. Review the CAD model of the workpiece, including its features, contours, curves, and dimensions. Identify areas of the workpiece that require machining on multiple sides or surfaces, as well as any complex geometries or non-linear features that may benefit from rotary axis machining. Consider the machining objectives, material properties, dimensional tolerances, and surface finish requirements when planning the machining process.
Selecting Suitable CAM Software for Rotary Axis Machining:
The next step is selecting suitable CAM (Computer-Aided Manufacturing) software that supports rotary axis machining capabilities. Various CAM software packages offer modules or functionalities specifically designed for generating toolpaths for rotary axis machining. Some popular software options include Autodesk Fusion 360, SolidWorks CAM, Mastercam, Siemens NX CAM, and CAMWorks. When selecting software, consider factors such as ease of use, compatibility with CNC machines, availability of advanced toolpath generation algorithms, and customization options to meet specific machining requirements.
Generating Toolpaths for Rotary Axis Machining:
Once the CAM software is selected, generate toolpaths for rotary axis machining based on the workpiece geometry and machining requirements. Utilize the software’s rotary axis machining capabilities to define toolpaths that incorporate rotary axis movements for machining operations on curved, contoured, or non-linear surfaces. Specify cutting parameters such as spindle speed, feed rate, depth of cut, stepover value, and tool orientation to optimize toolpaths for machining efficiency and surface finish quality. Experiment with different toolpath strategies such as 3+2 machining (positioning the rotary axis at fixed angles) or full simultaneous 4-axis/5-axis machining (allowing continuous rotary axis movement) to achieve desired machining outcomes.
Configuring Rotary Axis Parameters and Workpiece Setup:
Before executing the toolpaths on the CNC machine, configure rotary axis parameters and set up the workpiece on the machine table. Calibrate the rotary axis to ensure accurate positioning and alignment with the machine coordinate system. Define rotary axis limits, speeds, and accelerations to prevent collisions and ensure safe operation during machining. Secure the workpiece on the machine table using clamps, fixtures, or vacuum systems, ensuring stability and accessibility for rotary axis movements. Verify workpiece orientation and alignment with respect to the rotary axis to ensure proper machining results.
Performing Machining Operations and Monitoring Progress:
With the machine set up and toolpaths generated, execute the machining operations on the CNC machine, monitoring progress and performance throughout the process. Monitor spindle speeds, feed rates, cutting forces, and tool wear during machining operations to ensure optimal performance and machining quality. Utilize built-in monitoring systems or sensors to detect anomalies, tool breakage, or machine malfunctions and take corrective actions as needed. Collaborate with colleagues or supervisors to troubleshoot issues and optimize machining parameters for improved efficiency and quality.
Performing Post-Machining Inspection and Quality Checks:
After completing the machining operations, perform post-machining inspection and quality checks to verify dimensional accuracy, surface finish quality, and compliance with engineering specifications. Utilize precision measuring tools such as calipers, micrometers, and CMMs (Coordinate Measuring Machines) to measure critical dimensions, tolerances, and surface profiles of the machined parts. Conduct visual inspections to identify surface defects, burrs, or imperfections that may require further finishing or deburring. Document inspection results and track machining parameters for quality assurance and traceability purposes.
Implementing Best Practices and Safety Measures:
To ensure safe and efficient rotary axis machining operations, implement best practices and safety measures throughout the machining process. Some recommended practices include:
Regularly inspect and maintain CNC machines, rotary axes, tooling, and fixtures to ensure optimal performance and reliability.
Train operators and machinists on proper machine operation, tool handling, and safety procedures for rotary axis machining.
Establish clear protocols for machine setup, toolpath generation, workpiece loading, and machining operations to minimize errors and ensure consistency.
Provide adequate personal protective equipment (PPE) such as safety glasses, gloves, and ear protection to operators and personnel working in the machining area.
Adhere to industry regulations, safety standards, and best practices for machine guarding, lockout/tagout procedures, and hazard mitigation in the machining environment.
Conclusion:
Rotary axis machining is a versatile and powerful technique that enables CNC machinists to produce complex parts with precision and efficiency. By understanding the principles of rotary axis machining, selecting suitable CNC machines and software, analyzing workpiece geometry, generating toolpaths, configuring rotary axis parameters, performing machining operations, inspecting part quality, and implementing best practices and safety measures, machinists can master the art of rotary axis machining effectively. With the knowledge and skills acquired from this guide, machinists can expand their machining capabilities, optimize their processes, and achieve exceptional machining results in diverse industries and applications.