Mastering Piping System Design with AutoPIPE: A Comprehensive Guide
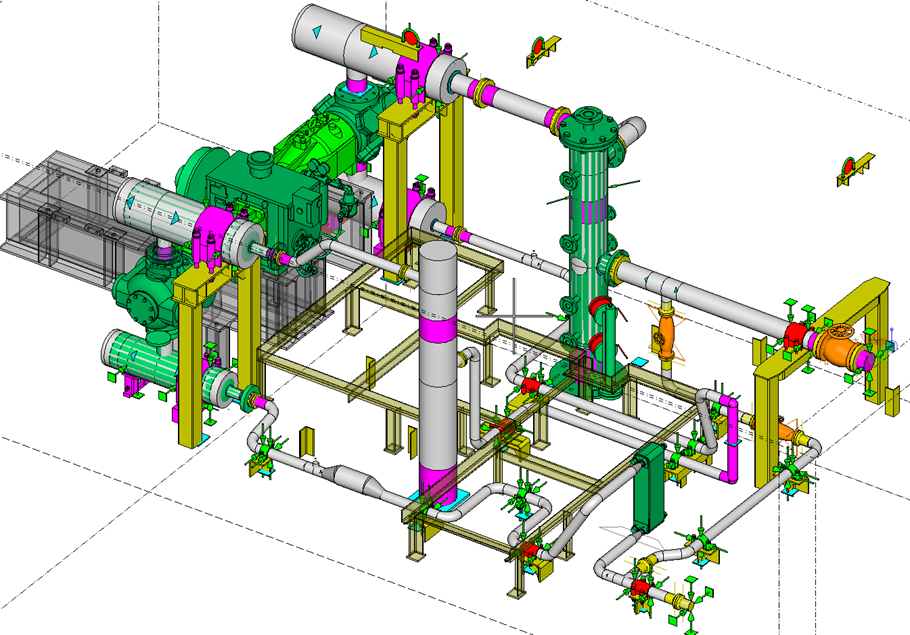
Introduction: Piping systems are essential components of various industrial facilities, including power plants, oil refineries, chemical plants, and HVAC systems. Designing piping systems requires careful consideration of factors such as fluid flow, pressure, temperature, material selection, and structural integrity to ensure safe and efficient operation. AutoPIPE, developed by Bentley Systems, is a leading software tool designed to assist engineers and designers in the analysis, design, and optimization of piping systems. In this comprehensive guide, we will explore the principles, methodologies, and best practices of designing piping systems in AutoPIPE, empowering professionals to create reliable and cost-effective piping designs for diverse engineering applications.
Section 1: Introduction to Piping System Design
1.1 Overview of Piping Systems: Piping systems are networks of pipes, fittings, valves, and accessories used to transport fluids (liquids, gases, or slurries) from one location to another within industrial facilities. Piping systems play a crucial role in various industries, including oil and gas, petrochemical, power generation, pharmaceuticals, and manufacturing, by facilitating the transfer of materials for processing, distribution, and storage.
1.2 Importance of Piping System Design: Proper design of piping systems is essential for ensuring the safe, reliable, and efficient operation of industrial facilities. Piping system design involves selecting appropriate materials, sizing components, determining layout configurations, and analyzing system performance to meet process requirements, regulatory standards, and industry best practices while minimizing costs and environmental impact.
Section 2: Overview of AutoPIPE Software
2.1 Introduction to AutoPIPE: AutoPIPE is a comprehensive software solution developed by Bentley Systems for the analysis, design, and documentation of piping systems. It offers a wide range of tools and features for performing static and dynamic analysis, stress analysis, code compliance checks, and design optimization of piping systems in various engineering applications.
2.2 Key Features and Capabilities: Familiarize yourself with the key features and capabilities of AutoPIPE, including geometric modeling, material selection, load generation, analysis settings, results visualization, and reporting tools. Learn how AutoPIPE’s user-friendly interface, intuitive workflow, and advanced analysis techniques streamline the process of designing and analyzing complex piping systems for diverse engineering projects.
Section 3: Designing Piping Systems in AutoPIPE
3.1 Geometric Modeling and Component Placement: Start by creating a geometric model of the piping system in AutoPIPE by defining pipe routes, component locations, and connection points. Use AutoPIPE’s drawing tools, CAD import capabilities, and library of standard components to model pipes, elbows, tees, valves, supports, and other piping elements accurately.
3.2 Material Selection and Specification: Specify material properties, piping specifications, and component details in AutoPIPE to accurately represent the physical characteristics of the piping system. Define material properties such as yield strength, modulus of elasticity, thermal expansion coefficient, and corrosion allowances to ensure compliance with design codes and standards.
3.3 Load Generation and Boundary Conditions: Generate loads and apply boundary conditions to the piping system in AutoPIPE to simulate operating conditions, environmental effects, and transient events. Define load cases, operating scenarios, thermal gradients, pressure fluctuations, seismic loads, wind loads, and other external forces to analyze system behavior under various loading conditions.
3.4 Static and Dynamic Analysis: Perform static and dynamic analysis of the piping system in AutoPIPE to evaluate structural integrity, stress distribution, and dynamic response. Use AutoPIPE’s analysis modules, including static analysis, modal analysis, harmonic analysis, time history analysis, and response spectrum analysis, to assess system performance and identify potential design issues.
Section 4: Advanced Analysis Techniques for Piping Systems
4.1 Stress Analysis and Code Compliance: Conduct stress analysis and code compliance checks in AutoPIPE to ensure that the piping system meets regulatory requirements, industry standards, and design criteria. Perform stress calculations, fatigue assessments, and code checks based on relevant design codes such as ASME B31.1, ASME B31.3, ASME B31.4, ASME B31.8, and other international standards.
4.2 Pipe Support Design and Optimization: Design and optimize pipe supports, hangers, and restraints in AutoPIPE to ensure adequate support and stability of the piping system. Analyze support locations, support types, load-bearing capacities, thermal expansion allowances, and seismic response to minimize stresses, deflections, and vibrations in the piping system.
4.3 Fluid Flow Analysis and Hydraulic Calculations: Perform fluid flow analysis and hydraulic calculations in AutoPIPE to evaluate flow rates, pressure drops, and energy losses in the piping system. Model fluid properties, flow regimes, pipe diameters, pipe lengths, fittings, and valves to optimize pipe sizing, minimize pressure losses, and improve system efficiency.
Section 5: Best Practices for Piping System Design in AutoPIPE
5.1 Model Validation and Verification: Validate and verify the piping system model in AutoPIPE through comparison with design drawings, specifications, and engineering calculations. Conduct model validation tests, sensitivity analyses, and benchmarking exercises to ensure that the simulated system accurately represents the physical behavior of the actual piping system.
5.2 Collaboration and Stakeholder Engagement: Foster collaboration and stakeholder engagement in piping system design projects by involving project stakeholders, design teams, construction teams, and regulatory authorities in the design process. Communicate design requirements, analysis results, and design recommendations effectively through presentations, reports, and interactive visualization tools to facilitate consensus-building, decision-making, and project approval.
5.3 Continuous Improvement and Professional Development: Stay abreast of industry trends, technological advancements, and best practices in piping system design and analysis to enhance your skills and expertise with AutoPIPE. Participate in training programs, webinars, conferences, and professional development activities to expand your knowledge, network with peers, and stay at the forefront of piping engineering and design.
Conclusion: Designing piping systems in AutoPIPE offers engineers, designers, and project stakeholders a powerful toolset for creating reliable, efficient, and cost-effective piping designs for industrial facilities. By mastering the principles, methodologies, and best practices outlined in this guide, professionals can leverage AutoPIPE’s advanced features and capabilities to model, simulate, and analyze complex piping systems with confidence and achieve positive outcomes in engineering design, construction, and operation. With proper training, collaboration, and adherence to industry standards, AutoPIPE empowers professionals to design piping systems that meet the needs of diverse engineering projects, ensure regulatory compliance, and optimize performance and safety in industrial environments.